January 29, 2025
In this blog: Contamination Risks | Responsible Recycling | Depackaging Technology | Your Partner in Innovation
Summary: This post explores the environmental risks of ineffective depackaging solutions for processing food waste into compost or digestate, and how the food industry can leverage data, training, and technology to prevent incidental packaging from polluting soil and water.
One of the biggest environmental challenges of managing unsold food is contamination and packaging. If we want to keep food out of landfills and effectively capture the energy and nutrient value for beneficial uses, then it is crucial that we responsibly separate food from its packaging with the right training and technology. All types of recycling and organics diversion programs are interdependent; how we manage one impacts how we manage all of them.
At Divert, we’ve found that by helping our customers manage unsold food products responsibly through training, data, and sophisticated depackaging technology, we can help them optimize diversion across many types of material.
In this post, we’ll explore how this strategy enhances diversion across all types of waste prevention, food donation recovery, organics diversion, and recycling programs.
Contamination Risks from Processing Unsold Food Packaging
Wasted food diversion programs reduce greenhouse gas emissions and support a circular economy by repurposing unsold food nutrients to regenerate our food supply chain. As new legislation emerges and more companies and municipalities increase their diversion, some organics processors are being inundated with more food material than they are equipped to handle.
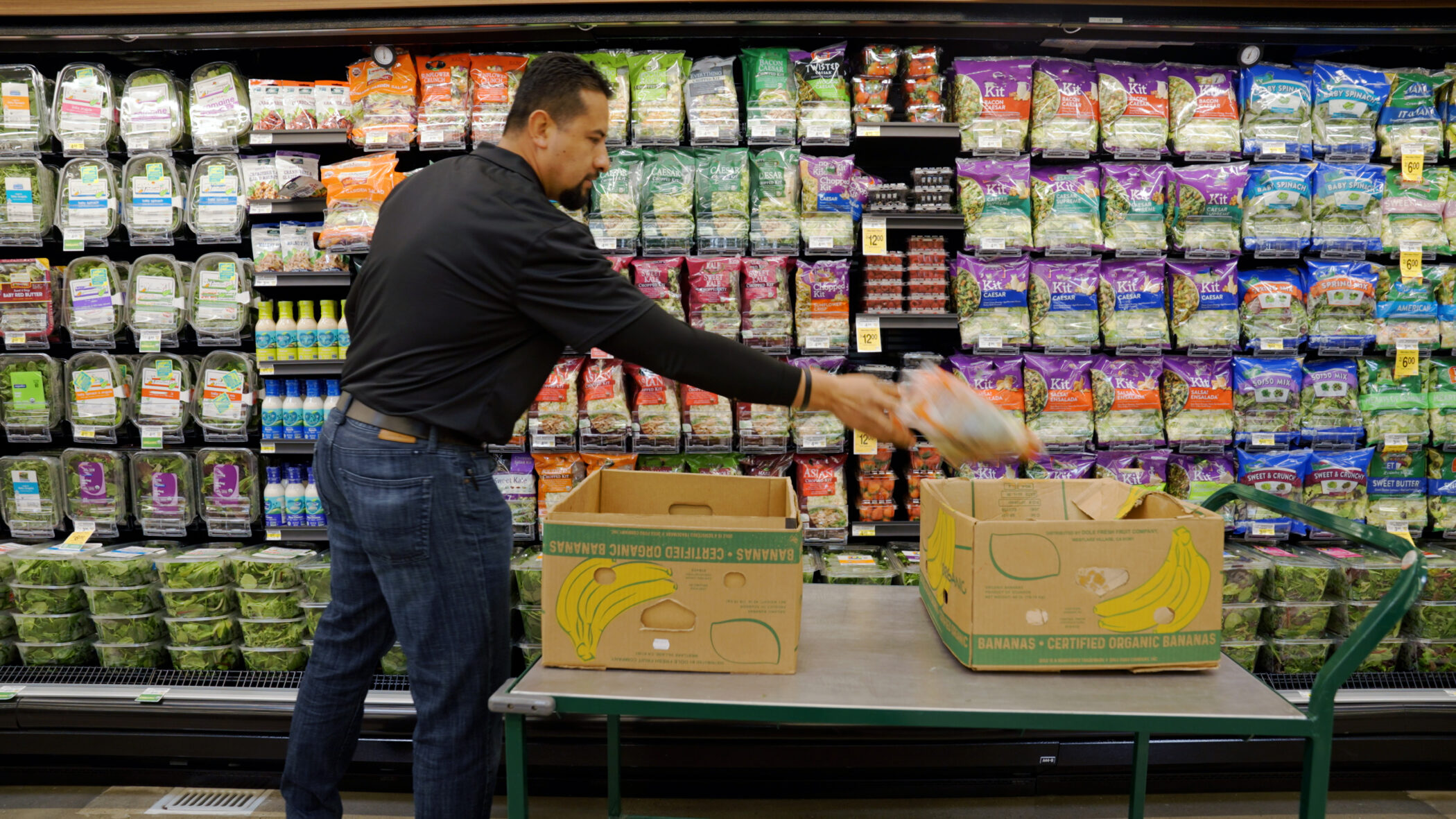
At the same time that organics processing is increasing, recycling standards for food packaging have narrowed. In 2018, China instated its Operation National Sword (ONS) policy, restricting its contamination standard to 0.05 percent and causing a global shift in how plastics are processed. Following China’s ONS policy, recyclers require clean feedstock. So, while pallets, cardboard boxes, shrink wrap, and other food packaging material can be accepted for recycling, the material that comes in direct contact with food cannot be recycled, such as containers of yogurt, produce stickers, bags of spinach, etc. Today, less than 9% of plastics are recycled globally; the rest goes to incinerators or landfills.
Much of food packaging material becomes an organics processing contaminant that cannot fully degrade through anaerobic digestion or composting. A study released in February 2024 by the Composting Consortium found that plastics contamination continues to be a significant challenge for the industry, with nearly half of composters finding trace amounts of conventional flexible plastic in their finished compost.
It’s critical that we don’t perpetuate another environmental problem while attempting to address one. To effectively scale diversion of food from landfills, we need a sophisticated, precise depackaging solution to help prevent food packaging material from polluting the soil that sustains our agriculture industry.
It’s critical that we don’t perpetuate another environmental problem while attempting to address one.
Fostering a Culture of Responsible Recycling
As consumers, we often think about the infrastructure around what goes out the front door of a store or restaurant –– how does food go from field, to cart, to kitchen? What is less often discussed is the infrastructure of what leaves the back door of a business –– how do food businesses know what to donate, recycle, or throw away?
Preventing recyclable material from being thrown away or processed with organic material starts with actionable data and in-store training. At Divert, we leverage our proprietary data and technology, and the expertise of our field teams, to build a communication loop with our customers and help them optimize this decision-making process. We’re able to monitor the contents of each Divert bin, report that data back to each store, and help them refine and reduce the material they send to our facilities to prevent donatable food and recyclable* packaging from being processed.
A major supermarket chain that partnered with Divert saw measurable results:
- 40% reduction in trash (approximately 82 tons per store, per year, kept from the landfill)
- 15% increase in donations (approximately 7,300 additional pounds donated per store, per year)
- 195% increase in processing food into renewable energy
- ~$8,000 per store, per year, in savings from trash costs
Innovative collaborations like Divert’s work with Feeding America are helping our customers take their waste reduction and food recovery goals even further: Divert’s data on what food is being wasted in retail stores and Feeding America’s data on what food retailers are donating can together create a clearer, more actionable picture for retailers to optimize their sales, donations, and diversion efforts.
Preventing Contamination with Sophisticated Depackaging Technology
Food packaging comes in an almost infinite variety of materials, shapes, weights, and densities, from tiny produce stickers to airtight cucumber sleeves, mesh produce bags, plastic jugs, and everything in between. The complexity of different types of food packaging makes it difficult to depackage that food by hand; even the most well-trained teams will not be able to achieve 100% purity of source separated organics, and in many cases, the results are significantly less. The technology that depackages wasted food needs to be precise in its ability to separate non-organic material from unsold food without shredding it and creating microplastics.
The complexity of different types of food packaging makes it difficult to depackage that food by hand; even the most well-trained teams will not be able to achieve 100% purity of source separated organics, and in many cases, the results are significantly less.
While there are turn-key, off-the-shelf depackaging solutions in market today (with varying degrees of effectiveness), Divert has engineered its own proprietary depackaging solution to reliably process wasted food on an industrial scale and more effectively reduce environmental challenges.
Divert’s proprietary depackaging technology works like this:
- A blade gently separates, but does not shred, nonbiodegradable packaging from organic material. This machinery is similar to a string press used for paper but is much less aggressive.
- Organic material is liquified into a slurry and screened multiple times with filters and membranes to remove contaminants and purify the slurry for anaerobic digestion.
Here are some of the key differences of Divert’s depackaging technology, compared with other solutions:
- Divert’s entire process takes place within an enclosed facility to minimize odors, greenhouse gas emissions, contaminants, and other negative effects.
- Our depackaging machine gently separates the organic material from the non-biodegradable packaging without shredding it to reduce packaging remnants from contaminating the resulting digestate.
- Divert’s wet process of creating and filtering liquid slurry is more precise and efficient than composting infrastructure, which tries to sift out plastic solids from organic solids. It also optimizes the amount of valuable carbon and nutrients captured to create a clean liquid slurry for producing renewable energy.
With this technology, we’re able to reliably process a much wider range of commercial food and organic waste streams, and optimize the energy and nutrient capture from the material to a greater degree, compared to other commercial operations that are utilizing turn-key depackaging units coupled with composting or co-digestion facilities.
Your Partner in Innovation: Divert
It’s time for a transformation in how we manage unsold food, and Divert is scaling the solutions to help our customers do that responsibly and effectively.
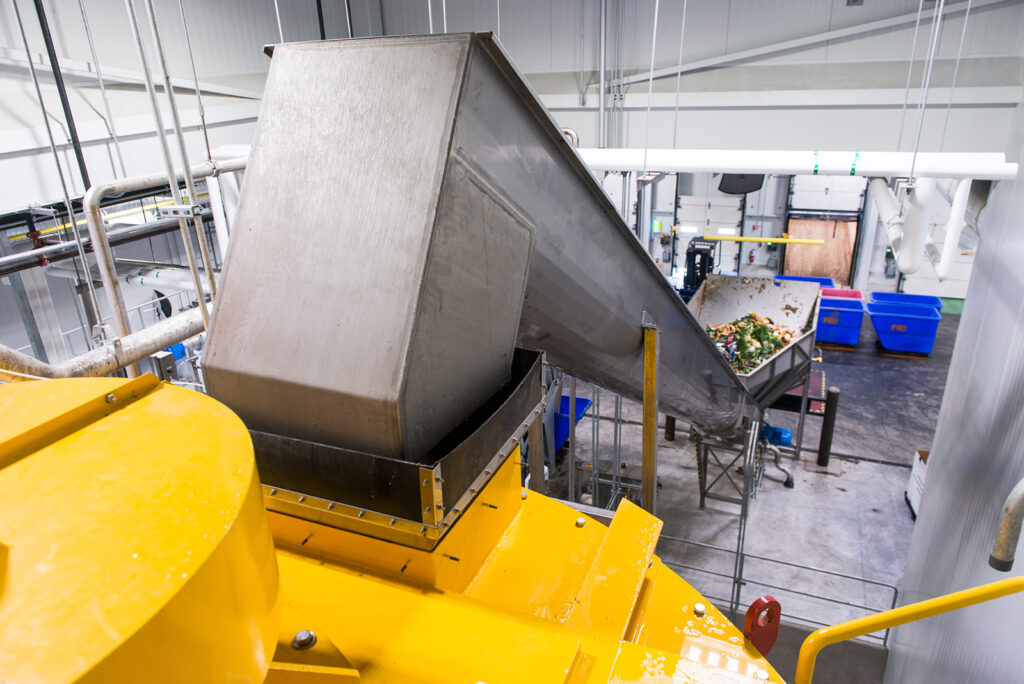
We’ve designed our diversion program to work in harmony with other recycling processes to help ensure that edible food reaches those who need it, inedible food goes to organics processing, and that other recyclable materials reach their intended destination to reduce the environmental impacts of waste.
Founded in 2007, Divert is a leader in innovating holistic solutions to the wasted food problem. We process unsold food on an industrial scale, serving nearly seven thousand, five hundred customer locations nationwide. To date, we’ve processed more than three billion pounds of wasted food and helped our customers donate the equivalent of 12 million meals to the food insecure. We’re trusted by the nation’s leading grocery retailers and food producers to process their unsold food, such as Kroger, Ahold Delhaize, Blue Diamond, Target, Safeway, and Albertsons. We take a consultative approach to helping each of these customers achieve their sustainability goals, with reverse logistics and backdoor pickup processes that integrate seamlessly with their operations.
The infrastructure, technology, and processes we’ve built have set new industry standards, helping our customers prepare for tomorrow’s regulations while meeting today’s requirements with confidence. Our advanced technology enables the products we produce to be free of contamination to a much greater degree than other anaerobic digestion and composting solutions on the market. When it comes to managing unsold food, businesses across the food industry can trust Divert to innovate and provide reliable, sustainable solutions that address environmental challenges and future-proof their operations.
* Recyclable: packaging that is not contaminated and can be accepted by a local jurisdiction’s recycling program.